業務改善、現場改善、生産性向上の支援を行っています。町工場出身の中小企業診断士G.F.Consulting代表上村です。
IE手法はGF式現場改善の原因究明・ムダ発見・稼働率測定において最も重要なものになります。
IE手法を用いて現場の現状分析を行う事で、原因を客観的に定量的に捉える事ができるのが特徴です。
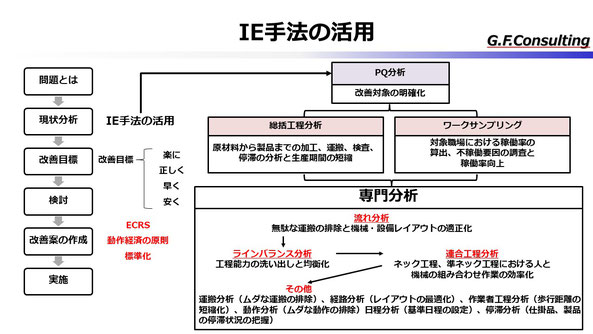
IE手法とは
IE((Industrial Engineering)とはインダストリアルエンジニアリングの略で、日本語では生産工学、経営工学といった表現をされます。
IEは広い意味で使いますが、 IE手法とはあくまで分析ツールとしての立ち位置だと考えて頂ければよろしいかと、
特に現場で使う上では原因究明のためのIE=分析と思ってください。
これは、ムダ発見や稼働率測定にも使えますので、多くの情報が集められ、原因究明が素早く行えるようになります。
実際に工場の中のダメな事ってなんとなくは誰でもわかるんですよね。
例えばその運搬作業必要?とか、その動きムダが多くない?とか。
でもそれってただの指摘ですよね。
そんなんじゃ経営者も、社員も「この作業は必要です。」「ムダな動きなんてありません。」という返しをしてくるかもしれません。
現状分析というのはいかに客観的で、定量的な事実を提示して、説得し、納得してもらうかにかかっています。
これは変化への抵抗とECRSで触れた通り、変化への抵抗への対処という事になります。
- 稼働率を定量的に捉え、見える化する事が出来る。
- ムダ作業を見つける事が出来る。
- 実際に時間などを計測するので、現場の納得感が
- 実施のために専門知識が必要
- 計測する人が必要になり、計測するための時間も多くかかる。
- 分析のための専門知識が必要
IE手法は気軽にやってみようというわけにはいきません。
本気で改善を行いたいのであれば、専門家に頼んで、現状分析をするのも一つの方法であると考えます。
その際にはIE手法などを使う事が出来る専門家か?というのを一つの基準にしてみるのも良いと思います。
定量的に捉えると専門家も改善効果について数字で語る必要があります。
専門家と〇%効率アップや、〇工程の稼働率を〇%にするなど、数字で合意をするとお互い緊張感を持った改善をする事が出来ると考えます。
PQ分析
IE手法では、一番最初にPQ分析を行います。
PQ分析とは横軸に品目、縦軸に生産量や出荷量をとって、生産品目を量の多い順に並べて比較したグラフです。
PQ分析では生産量の多い品目を抽出します。
なぜならば、生産量の多いものほど通常は改善効果が高いからです。
ですので、改善効果を高めるために、売上金額の面も考慮します。
ワークサンプリング
IE手法では、P-Q分析にて優先順位を決めた上で、ワークサンプリングや統括工程分析を行います。
ワークサンプリングは稼働分析を行うための瞬間観測法です。
ストップウォッチ片手に数時間観測するよりも、短い時間で観測できる事が利点です。
人の稼働率なのか、機械の稼働率なのかを決めておく事で着目すべき作業や動作を観測表の項目にしていきます。
自分の目に入った瞬間の作業などを観測表の項目に合わせチェックを入れていく形です。
必要観測数を決めて、ランダムな時間でとっていきますので、統計学的に精度を担保する事ができます。
<h2″>統括工程分析
IE手法の統括工程分析は分析の目的を決める事から始めます。
作業標準作成のためなのか、現場改善・生産性向上のためなのかを決めた上で、倉庫から完成品に至るまでのモノの流れを把握します。
その流れの中で加工〇、検査□、運搬➡、停滞▽などで表す事で、停滞や運搬を少なくする事が出来ないか検討していきます。
これらを行う事で在庫や、仕掛品を減らす事となり、隠れていた問題があぶりだされます。
問題を顕在化させるという事です。
特に現場作業の中の加工の割合の少なさに驚くクライアントが多いです。
その場合、運搬や停滞を改善していく事で確実に加工時間を増やす事ができ、成果を増やす事ができます。
まとめ
問題を認識し、原因究明する事で改善がしやすくなります。
IE手法は原因究明をする上で非常に有効なツールといえるでしょう。
原因究明する過程でムダ発見や、稼働率について知る事が出来ます。
原因の改善が定量的に行えるようになるため、改善効果の測定が正確になります。
IE手法は専門知識や実施する人・時間が必要となります。
専門家の活用も是非検討してみてください。